Exploring the Capabilities of Large-Scale 3D Metal Printers in Aerospace and Automotive Industries
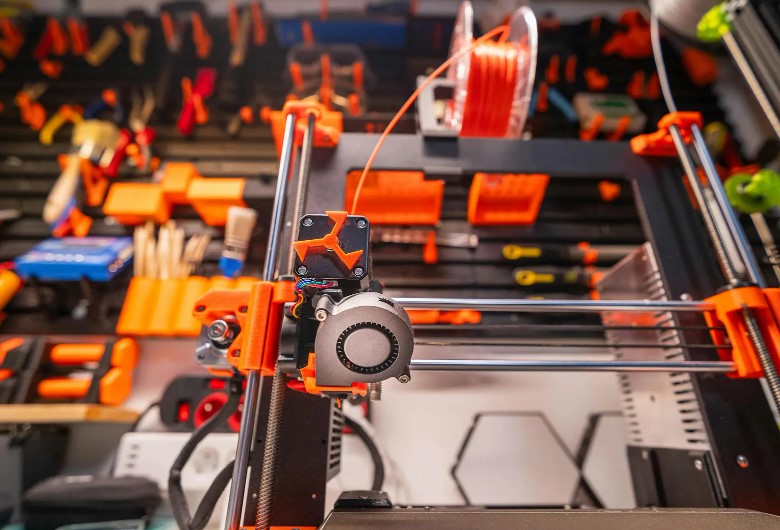
In a world where innovation drives progress, the aerospace and automotive industries are continually pushing boundaries. One of the most groundbreaking advancements powering this forward momentum is the use of large-scale 3D metal printers. These technological marvels are revolutionizing the way we manufacture parts, bringing unprecedented capabilities to industries that rely heavily on precision, strength, and performance.
Exploring the Rise of Large-Scale 3D Metal Printing in Aerospace
Large-scale 3D metal printing has become a game-changer for the aerospace industry. This cutting-edge technology allows the creation of complex components with unparalleled precision. Traditional manufacturing techniques often involve multiple steps and significant wasted material. In contrast, 3D metal printing builds parts layer by layer, reducing waste and optimizing material usage.
The ability to produce lightweight yet robust components is crucial in aerospace applications. This is where large-scale 3D metal printing shines. By using advanced materials, such as titanium and aluminum alloys, manufacturers can create parts that meet stringent industry standards while significantly reducing the overall weight of the aircraft. This not only enhances fuel efficiency but also contributes to the overall performance and safety of the aircraft.
Furthermore, the flexibility of 3D metal printing enables rapid prototyping and production of custom components. This is particularly valuable in the aerospace industry, where each part must meet exact specifications. With 3D metal printing, engineers can quickly iterate and refine designs, accelerating the development process and bringing innovative solutions to market faster.
Transforming Automotive Manufacturing with 3D Metal Printing
The automotive industry is also witnessing a transformation through large-scale 3D metal printing. Traditional manufacturing methods for automotive parts often involve complex tooling and assembly processes. 3D metal printing simplifies this by allowing the production of intricate components in a single step. This reduces the need for multiple parts and joints, resulting in stronger and more reliable structures.
One of the most significant advantages of 3D metal printing in the automotive sector is its potential for mass customization. Consumers today demand unique and personalized vehicles, and manufacturers must adapt to meet these expectations. With 3D metal printing, automakers can create customized parts and accessories on-demand, offering consumers a level of personalization previously unattainable.
Additionally, 3D metal printing enables the production of lightweight components that contribute to improved fuel efficiency and reduced emissions. By optimizing the design and material usage, manufacturers can create parts that are both strong and lightweight, enhancing the performance and sustainability of vehicles.
Understanding the Key Advantages of Large-Scale 3D Metal Printing
The adoption of large-scale 3D metal printing in the aerospace and automotive industries brings numerous advantages. One of the most notable benefits is the reduction in production time. Traditional manufacturing processes can be time-consuming, involving multiple steps and extensive lead times. 3D metal printing streamlines the production process, allowing for faster turnaround times and quicker delivery of finished products.
Another significant advantage is the cost savings associated with 3D metal printing. While the initial investment in 3D printing technology may be substantial, the long-term cost benefits are substantial. By reducing material waste, minimizing tooling, and optimizing production efficiency, manufacturers can achieve significant cost savings over time.
Furthermore, 3D metal printing enhances supply chain resilience. Traditional manufacturing often relies on a complex network of suppliers and logistics, which can be vulnerable to disruptions. With 3D metal printing, manufacturers can produce parts in-house, reducing dependence on external suppliers and mitigating supply chain risks.
Pioneering Innovations in 3D Printing
With years of dedicated research and development, AML3D has emerged as a leader in the additive manufacturing revolution. Their team of experts has combined advanced welding techniques with robotics and software applications to create an automated 3D printing system that can create freeform prototypes for various industrial applications. They are proud to offer the world’s largest, commercially available, open-air, production-ready metal 3D printers.
Their innovative approach to 3D metal printing has opened new possibilities for the aerospace and automotive industries. By leveraging their advanced technology, manufacturers can achieve greater precision, efficiency, and flexibility in their production processes.
Read also: How Do 3D Billboards Work? Unveiling the Technology Behind the Visual Marvel
Exploring Future Trends in 3D Metal Printing
The future of large-scale 3D metal printing in the aerospace and automotive industries is promising. As technology continues to evolve, several trends are likely to shape its trajectory. One such trend is the increasing adoption of multi-material 3D printing. This involves the use of different materials within a single print, allowing the creation of components with varying properties. This capability is particularly valuable in applications where different sections of a part require different mechanical characteristics.
Another trend is the integration of artificial intelligence and machine learning in 3D printing processes. AI algorithms can optimize print parameters, monitor production in real-time, and predict potential issues before they occur. This enhances the reliability and efficiency of 3D printing, further driving its adoption in critical industries.
Sustainability is also becoming a key focus in 3D metal printing. The ability to produce lightweight components with minimal waste aligns with the growing emphasis on sustainable manufacturing practices. Manufacturers are exploring ways to use recycled materials and develop more eco-friendly printing processes to reduce their environmental footprint.
Addressing Challenges in 3D Metal Printing
While large-scale 3D metal printing offers numerous benefits, it also presents certain challenges. One of the primary challenges is the need for post-processing. Printed components often require additional finishing steps, such as machining or heat treatment, to achieve the desired surface quality and mechanical properties. Manufacturers must invest in post-processing capabilities to ensure that printed parts meet industry standards.
Another challenge is the development of standardized testing and certification protocols for 3D-printed components. In industries like aerospace and automotive, where safety and reliability are paramount, rigorous testing and certification processes are essential. Collaborative efforts between manufacturers, regulatory bodies, and research institutions are needed to establish comprehensive standards for 3D printed parts.
Despite these challenges, the potential of large-scale 3D metal printing to revolutionize manufacturing remains undeniable. Continued advancements in technology, materials, and processes will address these challenges and unlock new opportunities for innovation.
Embracing the Future of Manufacturing
The integration of large-scale 3D metal printing in aerospace and automotive industries represents a significant leap forward in manufacturing capabilities. The ability to create complex, lightweight, and customized components with precision and efficiency is transforming the way products are designed and produced.
Manufacturers that embrace this technology gain a competitive advantage by reducing production times, lowering costs, and enhancing product performance. The versatility of 3D metal printing allows rapid prototyping, on-demand production, and mass customization, meeting the evolving demands of consumers and industries.
Large-scale 3D metal printing is reshaping the landscape of aerospace and automotive manufacturing. Its ability to deliver high-quality, innovative solutions with speed and efficiency positions it as a crucial tool for the future. By leveraging the expertise of pioneers and staying attuned to emerging trends, manufacturers can harness the full potential of 3D metal printing to drive progress and achieve new heights in their respective industries.